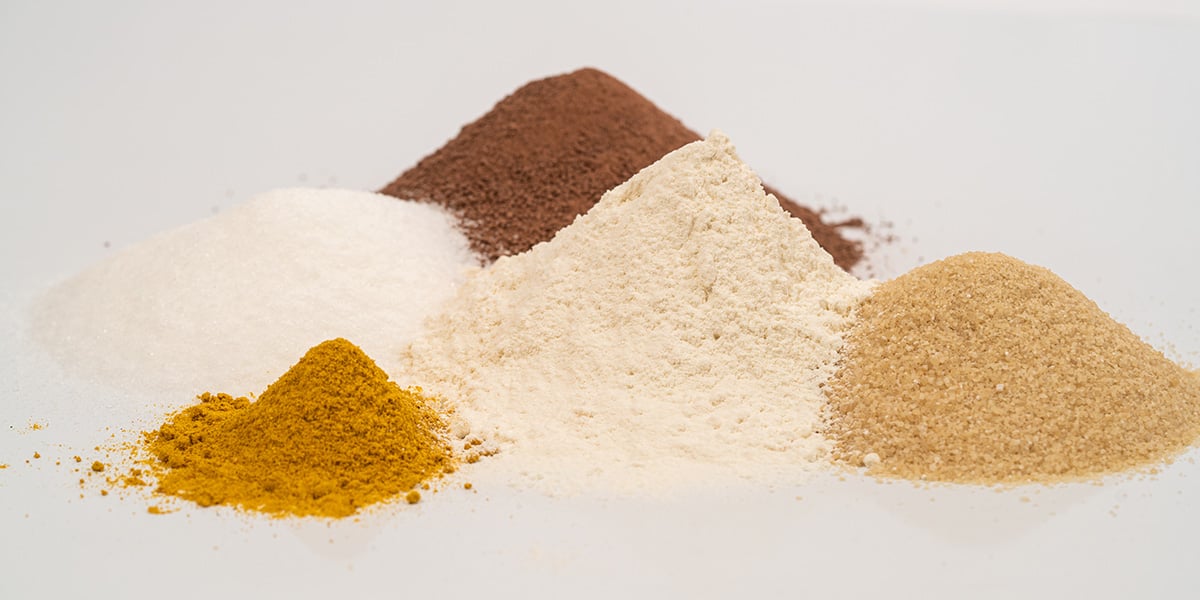
Essentials of Powder Packing
When it comes to packaging for powder products, it is of the utmost importance to take the right approach.
After all, products that come in powder form – as is the case for many nutrition products, pharmaceuticals, and so on – come with their own particular needs.
So, what are the most crucial things to know about powder filling and the associated packaging? Below, we explain the key elements.
Introduction To Powder Filling
The term “powder filling” may seem self-explanatory enough; it refers to the process whereby dry powder is measured and dispensed into containers.
Powder filling occurs in a variety of industries, such as food, cosmetics, pharmaceuticals, and chemicals. While these sectors may differ markedly, one thing they have in common is that end users expect the final product to be high in quality, safe to use, and robustly packaged.
The packaging for powder products has not, of course, always been the same. Over the years, significant advancements have been made in powder packaging and filling, which have been instrumental in streamlining production processes and maintaining product safety.
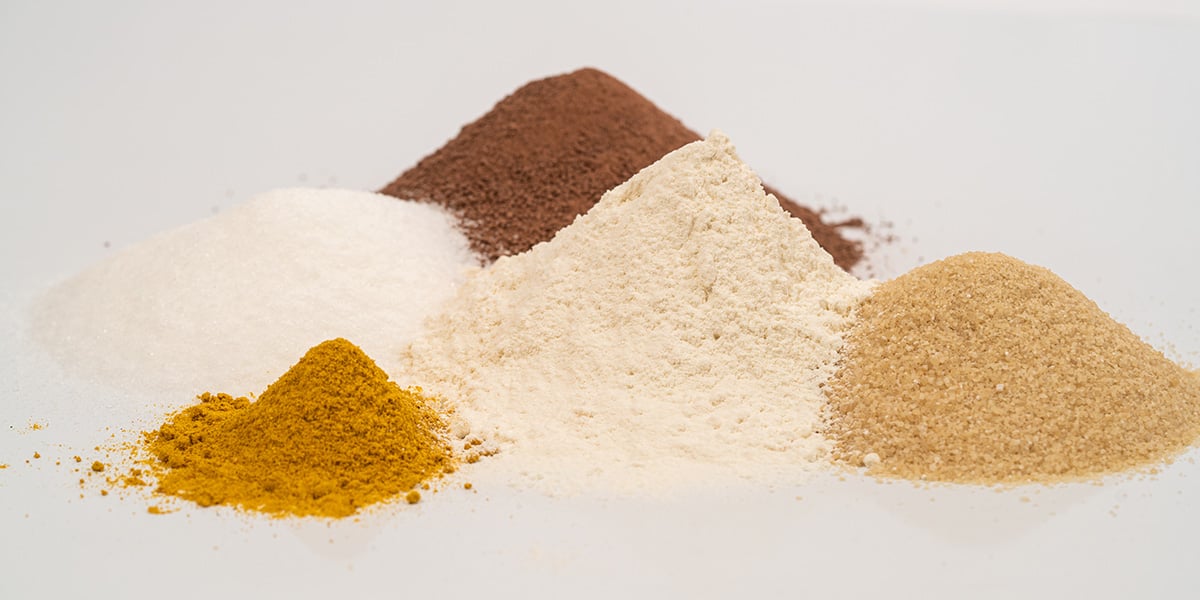
Key Techniques and Methods Used
Through the years, various powder filling methods and techniques have been developed and refined to help ensure the greatest possible efficiency, accuracy, and consistency.
A major theme has been the emergence and development of ever-more sophisticated powder filling machinery and automation.
Below are some key methods that have long helped create the best-quality powder packaging for all manner of items:
· Volumetric filling
This process uses a machine to fill a container with a precisely measured amount of powder.
This method is proven to be effective in filling containers with a consistent volume of product, even as the exact sizes and shapes of those containers can vary.
Volumetric filling is an efficient means of filling a broad range of different containers, such as bottles, pouches, and boxes.
· Auger filling
As the name indicates, this procedure entails the use of a helical screw – or “auger” – to precisely measure out the required quantity of a powder product, before dispensing it into a container.
So, as you can probably imagine, the ability to specifically control the amount of product filled is a big advantage of auger filling.
Auger filling machines have long been used for filling and packaging a wide range of dry powdered goods, such as spices, coffee, sugar, salt, detergents, and pharmaceutical powders.
· Aseptic powder filling
The need for various pharmaceutical powders to be kept sterile helps draw attention to the critical role that aseptic powder filling plays in the manufacturing of such sensitive products.
This process involves the filling of containers in a controlled environment, to guard against microbial and particulate contamination.
Aseptic powder filling, then, is vital for making sure the given product is pure, safe to use, and effective.
Common Applications Across Industries
Many different industries rely on powder packaging and filling. These encompass the likes of:
· Pharmaceuticals
With the broad range of powdered products in this specialised sector including such often essential items as medicines, vitamins, supplements, and energy boosters, it is clearly vital for the safety and integrity of these products to be of the very highest standards.
Achieving this depends on the right packaging being chosen for such products, as well as the most suitable and stringent powder filling processes being followed.
Of particular importance for the powder filling of many pharmaceutical products, is the achievement of a sterile environment that protects against contamination.
· Food
There is a need in the food industry to package products such as protein powders, spices, flour, and powdered milk in ways that protect them from external elements. This, in turn, helps preserve the nutritional value of such foods, while boosting their shelf life.
Machines including auger fillers and vacuum fillers are used to measure and dispense powdered food products into containers such as cans, bottles, bags, and pouches.
· Personal care
Many consumers use common personal care products daily, such as baby powder, makeup, and eye shadow, with the expectation that they will consistently meet high-quality standards.
The right filling processes and packaging for powder products like these allow for such expectations to be met, time and time again.
Products in this sector come in many different pumps, jars, and other containers. Powder filling machines play a critical role in achieving the necessary product quality, safety, and efficacy.
Advantages And Challenges of Powder Filling
The powder filling and packaging processes that are in use today present invaluable advantages to a wide range of industries, but also some undoubted challenges.
Advantages
The below benefits are possible when the most sophisticated filling procedures and packaging for powder products are used:
· Precision
Today’s leading powder filling machines are capable of filling containers with a remarkable level of accuracy and consistency.
In the current world of highly automated systems, the exact weight of the given powder can be quickly measured before the required amount of it is moved into the container.
· Reduced waste
The high-performing and impressively functional powder filling machinery in widespread operation today is able to accurately measure and dispense the given powdered product into containers. This consistent precision greatly helps reduce waste over time.
The weighing systems commonly used for powder filling have never been more accurate than they are now. This, combined with fast and efficient automation, has contributed greatly to minimising waste.
· Improved product safety
There are certain sectors – such as the pharmaceutical industry – where maintaining stringent hygiene standards is an especially critical priority. After all, any failure to meet such standards could put the safety of the given product’s end users at risk.
To this end, the current industry-leading automatic powder filling machines incorporate such features as closed filling mechanisms and dust-proof systems, to ensure continued sterility and to protect against any risk of contamination.
Challenges
Such factors as weight, air, and powder flow can potentially pose challenges to organisations’ day-to-day powder filling and packaging processes.
· Handling powders with varying densities
“Density”, of course, is not the same thing as weight – the term refers to the concentration of a substance within a given volume.
It is important to be aware of this factor because of, for example, the tendency for powders of different densities to segregate when efforts are made to blend them.
This may necessitate the use of specialised mixing techniques in order to achieve a homogeneous blend.
· Ensuring sterility
We have referenced sterility a number of times in this article, and for good reason. Particularly as far as pharmaceuticals are concerned, it can be critically important to ensure there are no potentially harmful microbes in the environment where a given powder product is being packaged.
In such situations, a tightly controlled environment is essential. This typically necessitates the use of powder filling machinery that has been specifically designed with sterility and hygiene concerns in mind, as well as arrangements to sterilise containers and raw products separately.
· Maintaining equipment efficiency
Achieving the highest possible levels of efficiency will always be of great importance when it comes to powder filling and packaging.
Fortunately, there are many ways to achieve this. They range from ensuring the right machinery is being used and the adjustment of machine settings, right through to well-targeted process optimisation and preventative maintenance of powder filling equipment.
Industry Standards and Best Practices
There are various industry standards, guidelines, and broadly accepted good practices that affect the filling processes and packaging for powder products.
Adherence to these standards isn’t merely “recommended” or a “good to do” for manufacturers. Complying with such requirements is of huge importance for such purposes as quality assurance, safety, driving down costs, and maximising efficiency.
So, if your organisation manufactures powdered products, it is crucial to maintain up-to-date knowledge on relevant standards such as:
· Good Manufacturing Practices (GMP)
These are guidelines applicable to all elements of the production of powdered medicinal products, encompassing the materials, equipment, and people involved.
As of today, more than 100 countries have incorporated the World Health Organization (WHO)’s GMP provisions into their national pharmaceutical regulations.
· International Organization for Standardization (ISO) standards
In the words of ISO itself, an ISO standard can be broadly defined as “a formula that describes the best way of doing something”, as internationally agreed by experts.
If, then, your organisation is involved in powder filling and the manufacture of powdered products, you will have good reason to pay close attention to the most relevant ISO standards.
Achieving compliance with such standards could be instrumental in your business’s ongoing efforts to bolster efficiency, streamline costs, and optimise environmental performance.
Conclusion
In putting together this article, we have sought to give a sense of what powder filling is, the various forms that powder filling machinery takes, and the benefits and challenges associated with these processes that are becoming ever-more automated today.
During the 2020s, efficient and safe powder filling operations remain of the very greatest importance across a broad range of industries.
Here at WePack, we would urge you to further explore the professional solutions that could represent the right match to your own business’s powder packaging requirements.
To learn more about the role that we could play in this as contract packing specialists, please don’t hesitate to contact us.