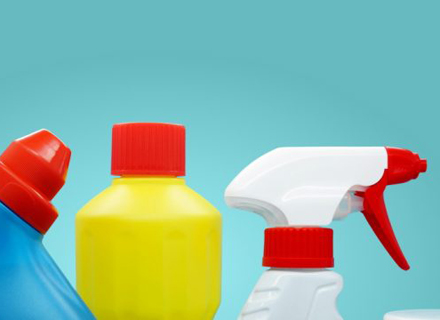
Packing liquid products: what factors must be considered?
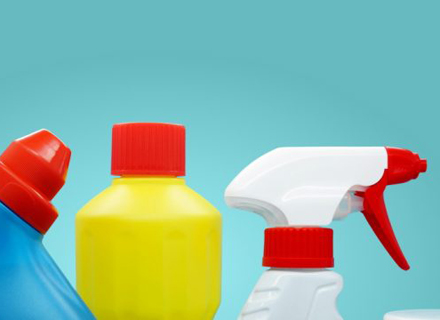
Packing liquid products: what factors must be considered?
The planning required to pack liquid products into the correct containers can mean the difference between merchandise arriving quickly on shelves or the potential spoilage of goods, and possible legal issues.
This can be challenging for companies without the time, equipment or skills to follow the required series of precise steps. Failing to follow stringent regulations can result in faulty packaging, contaminated product, and even put employees and customers in danger.
Instead of tackling the job in-house, some companies may choose the route of a contract packing service to reduce risks of litigation and recalls.
Tell WePack about your project!
What packing material should be used?
Materials can affect a product’s quality, preservation and safety. There are also several different packaging options available, so it’s important to get this right.
Mick Clark, Managing Director at contract packing company WePack, said: “Make sure you don’t confuse PET (Polyethylene terephthalate) with PVC (Polyvinyl chloride). Aggressive cosmetics are often stored in PET bottles. But if you put acetone in a PVC bottle it would attack the material and only last about 10 minutes before melting.”
Most plastics are porous, which can cause potent scents (such as perfumes) to escape and air to seep through. This can reduce the shelf-life of some liquids—such as alcoholic beverages—or cause them to spoil completely. However, this is not the case with glass bottles.
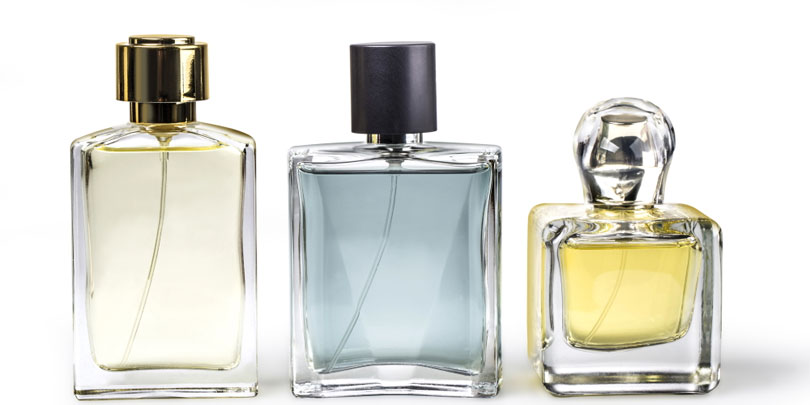
“Glass is suitable for most liquids and is reusable and aesthetically pleasing. But it’s inflexible, breakable and heavier, which can create problems during transportation,” Mick continued.
Cosmetic liquids are often stored in PET or glass jars. Gas flushing may be required for bottles containing solvents such as nail polish remover. This process involves the repeatedly injection of inert gases (carbon dioxide or nitrogen) into the packaging, which is then flushed out to remove all the oxygen. The procedure helps prolong the liquid’s shelf life and protect it from damage. It also prevents strong scents from escaping and strengthens the bottle’s internal walls.
Mick said: “Liquids are often kept in bottles, jars, tubes or sachets. To determine which option is suitable for the product, speak with the contract packing firm.
“Another reason companies may outsource their liquid filling to a specialist is the need for correct equipment for specific jobs. There are a number of different liquid filling machines to suit each type of liquid consistency.
“Honey needs to be packed slower and warmed. Nail polish remover is runny and fills fast. Hand cream and gels fill fast, but shouldn’t be filled too fast otherwise air may be added when not needed.”
Packing dangerous liquids
Some hazardous liquid products may require employees to wear personal protective equipment (PPE). This can include gloves, mask, overcoat and visor to protect the eyes from splashing.
Mick added: “Discuss the necessary level of protection with the contract packing firm. They will need proper safety equipment and machinery to complete the job without putting anybody at risk.”
Hazardous liquids can include cleaning chemicals, gases and acid.
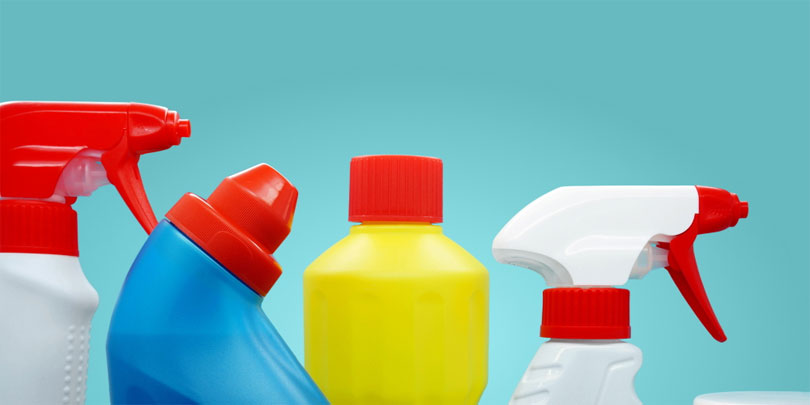
“If there is only a small number of hazardous products to pack, a packing company is unlikely to take on the job.” Mick continued: “If it needs doing in-house, any staff handling toxic liquids must be sufficiently protected and qualified.”
When packing flammable fluids, companies must ensure the filling machines do not have an ignition and are non-electrical.
Most critical hazardous liquids need a MSDH (material safety data sheet). This supplies workers with the correct measures to safely handle and work with a certain substance, such as the necessary protective equipment, first aid recommendations, technical instructions and storage and disposal suggestions.
Employers handling dangerous substances must follow The Dangerous Substances and Explosive Atmospheres Regulations 2002 (DSEAR) to protect the workplace and members of the public from any risks of fire, explosion and corrosion of metal.
Companies that supply any hazardous chemicals within the EEA must also abide by the Classification, Packaging and Labelling of Chemical Substances and Mixtures regulations, which complements the REACH regulations.
Prevent leakages
Liquids can easily leak if the proper precautions are not taken. The products must be checked throughout the process up until they are shipped, to make sure the packaging is secure.
Mick said: “Sticky liquids will completely wreck the other products around them if they leak. It’s not critical if it’s water, but it is if it’s honey. If the product is runny, a leak will become obvious very quickly.
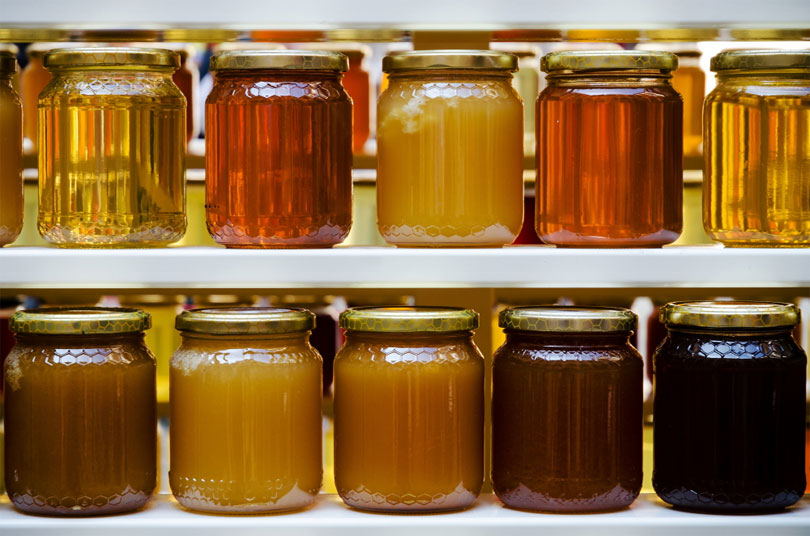
“Most leaks are a result of faulty closures. They need tightening to the correct torque settings to prevent them from coming off during transit. Discuss this with the packing firm, as this varies depending on cap size.”
Wine and spirit bottles should be securely sealed, which often requires cork cap presses or capping machines
Mick added: “Caps should be frequently checked as they can loosen over time. For further protection, a plastic seal can be placed over the cap. Secure sealing prevents any contaminations entering the packaging.”
Packing food liquid products
Any company handling bare or raw food liquids needs a certificate to show that hygiene and safety regulations are being followed.
“When looking for a contract packing company to handle food products, visit the facility to check that it is hygienic, safe and suitable for your requirements,” said Mick.
“Ask about the hygiene procedures they follow to keep the environment and equipment clean, and how they prevent bacteria cross-contamination.”
BRCGS is a Global Food Safety Initiative-recognised brand and consumer protection scheme which provides an accreditation to companies handling raw food sold in supermarkets. This rigorous scheme ensures manufacturers meet their legal responsibilities to safeguard the end-customer.
Mick added: “Not all companies have the budget for this expense, and will need to collaborate with fully food-certified contract packing firms instead.”
The UK currently complies with the EU legislation on food contact materials. This includes providing a written declaration of compliance (DOC) for some types of food contact materials, such as plastics. If necessary, companies can request to see this documentation.
Mick said: “It’s generally safe to pack food products in aluminium, but it may not react well with acidic foods such as citrus fruit juice. Food is commonly packed in plastic such as PET. However, PVC is often avoided as it can contain hazardous ingredients.”
Temperature requirements for packing alcohol
Alcoholic beverages that need storing at the packing facility for a certain period must be kept in a temperature-controlled environment.
Most wines shouldn’t be stored in warm environments, as this can weaken and flatten the flavours. The heat can also expand wooden corks, which could possibly spoil the wine and lead to leakages.
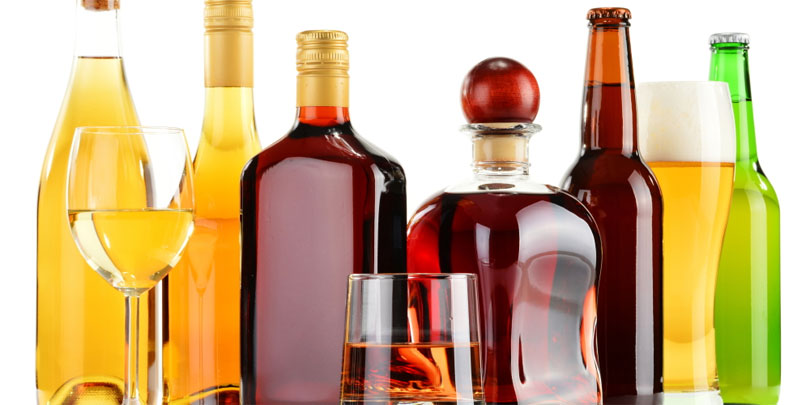
Spirits can usually be stored at room temperature but keeping the product relatively cool can preserve them for longer. Heat can make spirits expand and evaporate quicker, altering the taste over time.
Research by Bacardi suggests exposure to ultraviolet light can dramatically change the colour of some spirits stored in clear bottles within days.
Warm temperatures can prematurely age craft beer, so keep these products chilled to retain their freshness.
Transporting liquid products
It’s essential that liquid products arrive at their final destination in perfect condition when shipped in bulk. Fragile products may need protective packaging to prevent any damage during transit; for example, boxes holding glass bottles can be fitted with card dividers or corner posts. Heavy products are also often double-wrapped.
Mick added: “The packing firm should do a final quality check of the products before they are transported to make sure they are as secure as possible.”
Packing liquid products in bulk can be complex. Without the necessary qualifications, accreditation and equipment, mistakes can be easily made which have detrimental consequences. But trusting a packing company to meet specific project requirements will allow you to focus on your everyday practices and put your mind at ease.
To find out more about our packing services please contact WePack on 0115 852 9000 or get in touch via the form below.